Variantenproduktion - Niedrige Durchlaufzeit trotz hoher Variantenvielfalt
Wie Durchlaufzeiten in der Variantenproduktion bei komplexen Produkten reduziert werden können
Die steigende Produktvielfalt und damit einhergehende Komplexität in der Variantenproduktion resp. Variantenfertigung, ist ein Problem mit dem sich, mehr oder weniger ausgeprägt, fast jedes Unternehmen befasst. Die Ausbringungsmenge bleibt unter dem eigentlichen Niveau, der Aufwand in der Angebots- und Auftragsabwicklung ist höher als nötig und die Kundenzufriedenheit bzgl. Lieferzeit und Liefertreue könnte auch besser sein. Intuitiv wissen diese Unternehmen häufig, woran das liegt. Die Komplexität der Prozessabläufe und wechselnde Engpässe verstellen aber den Blick auf die Lösung. Die Hürde besteht darin Kundenanforderungen zu erfüllen, ohne die internen Aufwände und damit Komplexität zu steigern sowie die Liefer- und damit Durchlaufzeit zu verringern.
Umfragen hinsichtlich wichtiger Kundenanforderungen an den Vertrieb, als auch an die Produktion lassen sich nach wie vor in einem Satz zusammenfassen: Schnell und kostengünstig individuelle Kundenprodukte in hoher Qualität. Also grundsätzlich nichts Neues, denn das war gestern schon so und wird auch morgen noch so sein. Neu hingegen sind die deutlich gestiegenen Anforderungen an Variantenflexibilität bei hoher Lieferbereitschaft und damit kurzen Durchlaufzeiten. Maschinenbauunternehmen können sich der Forderung nach einer Produktpalette mit zahlreichen Varianten nicht entziehen [3]. Wenn daher die vom Markt geforderte Vielfalt kaum vermieden und auch nicht reduziert werden kann, bleibt nur der Weg, entstehende Komplexität zu beherrschen, und das sowohl in der Angebots- und Auftragsbearbeitung, als auch in der Produktion.
Branchen wie der Maschinen- und Anlagenbau nutzen modulare Produktstrukturen, die maßgeblich die Generierung von Skaleneffekten in Baugruppen und Einzelteilen unterstützen, ohne die vom Markt geforderte Vielfalt deutlich einzuschränken. Unter Modulen wird dabei die Zusammensetzung von Einheiten (Modulen) verstanden, die unabhängig voneinander konstruiert, gefertigt und geprüft werden können, aber erst in Kombination als zusammengehörige Einheit funktionieren [2]. Gleichzeitig sind deutliche Kostensenkungen in Herstell- und Prozesskosten realisierbar. In einigen Branchen wie der Automobilindustrie oder dem Maschinen- und Anlagenbau funktioniert dies über leistungsstarke Produktstrukturen wie Plattformstrategien und Baukastensysteme. Kosten- und variantenoptimierte Produktbaukästen machen es möglich, durch geschickte Kombinatorik, aus definierten Bausteinen eine Vielzahl von kundenangepassten Endartikeln zu generieren. Somit wird einerseits der Forderung nach kundenindividuellen Produkten zu Preisen von Serienartikeln Rechnung getragen, andererseits bleiben die interne Komplexität und damit Aufwände in der Angebots- und Auftragsabwicklung unter Kontrolle. Durch die generierten Skaleneffekte können sowohl Herstellkosten, als auch Durchlaufzeiten erheblich gesenkt werden. Plattform- und Baukastenstrategien, Standardisierung und Modularisierung sind ganz wesentliche Ansätze, um die Variantenvielfalt auf Baugruppen- und Teileebene zu reduzieren bzw. ganz zu vermeiden und damit nicht nur Kosten, sondern auch vor allem Zeiten zu reduzieren. Dazu bedarf es zum einen intelligenter Prozesskonzepte mit optimierten Abäufen, und zum anderen leistungsfähiger Software.
Um sich der Thematik systematisch zu nähern, werden zwei Bereiche wie folgt betrachtet:
- Produktstrukturperspektive: Portfolio, Produktsystem und Produktstruktur
- Prozessperspektive: Konfiguration, Prozesse und IT
Portfolio, Produktsystem und Produktstruktur im ganzheitlichen Variantenmanagement
Unter einem konfigurierbaren Produktsystem wird nach Markt- und Wertschöpfungssicht ein fragmentiertes und strukturiertes Produktprogramm verstanden, welches in Architektur und Produktstruktur systematisch und ganzheitlich aufgebaut wurde. Hierbei werden folgende Methoden zielgerichtet angewendet:
• Produktprogramm und Typisierungsformen nach Scope und Scale
• Architektur des Produktprogramms bzw. der Plattform
• Modularität nach Funktionen und mechatronischen Ansätzen
• Standardisierungs-, Bündelungs- und Gleichteilestrategie
• Produktordnungssystematik und Lösungsräume samt Konfiguration und Parametrisierung
In einem definierten Angebots- und Auftragsprozess mit sinnvoll eingesetzter, intelligenter IT-Unterstützung können Angebote und Aufträge effizient erstellt werden. Durch die Reduzierung der Komplexität in Produktstrukturen lassen sich Bearbeitungs- und Durchlaufzeiten enorm verbessern.
Eine der größten Hürden zu erfolgreichen Konfigurationsplattformen besteht im Aufbau und in der Strukturierung eines möglichst geschlossenen und upgradefähigen Produktsystems mit stabilen „Lego-Bausteinen“ (Modulen). Die meisten Maschinen- und Anlagenbauer haben neben endausgeprägten Lego-Bausteinen auch konstruktiv kundenspezifische Anpassungen in der Auftragsbearbeitung vornehmen. Es gilt demnach zu klären, wo sich der Aufwand einer Konfigurationslösung lohnt, und wo sinnvollerweise eine Abgrenzung vorgenommen wird und lediglich die Schnittstelle vorgegebenen Standards genügt. Erfolgreiche Anwender der Produktkonfiguration wie z.B. Krones, Siemens, SEW-Eurodrive, Lenze, Rittal oder KSB sowie viele mittelständische Maschinenbauunternehmen haben gelernt, mit diesen Herausforderungen tagtäglich umzugehen. Es gilt der Grundsatz: „Soviel Standardisierung wie möglich, soviel Fexibilität wie nötig“ [1].
Bei der Betrachtung von Kostensenkungszielen muss folgendes unbedingt beachtet werden: Modulare Produktstrukturen wirken i.d.R. stark positiv auf Prozesskosten, aber teilweise negativ auf Einzelkosten. Der positive Effekt auf Einzelkosten wird nur durch Skaleneffekte der Standardisierung erreicht, die in der Umsetzung durch geschickt gewählte Modularitäten und geeignete, auf Wertschöpfung und Beschaffung abgestimmte Produktstrukturen zu realisieren sind. Späte Kundenkopplung und späte Variantenentstehung sind dabei die Grundlagen, die ein Entwickler verstanden haben sollte. So entsteht eine Spreizung bzw. ein Trichtermodell zum Markt.
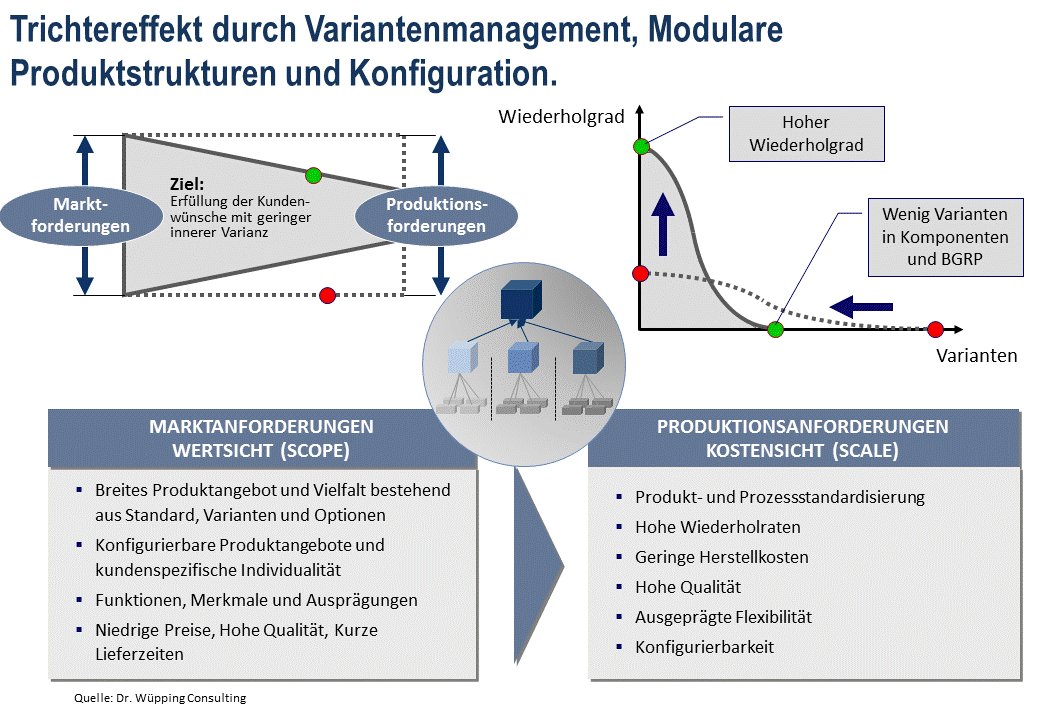
Bild 1: Abgleich interner und externer Anforderungen durch flexible Produktstrukturen.
Durch den erhöhten Wiederholgrad und die damit verbundene reduzierte interne Vielfalt werden Durchlaufzeiten in der Angebots- und Auftagsbearbeitung im Schnitt zwischen 30 und 50% reduziert. In Einzelfällen sogar deutlich höher. Hinzu kommt eine Reduzierung der Teilevielfalt von 30 % bei der Überarbeitung bestehender Maschinen und bis fast 70 % bei kompletten Neuentwicklungen.
Konfigurationsmethode, Prozesse und IT
Kundenspezifische Anforderungen verursachen i.d.R. höhere Konstruktions- und Herstellkosten und erhöhen die Durchlaufzeit bis zur Fertigstellung. Die Lösung besteht darin durch Kombination von bestehenden einzelnen Modulen, verschiedene Produktvarianten zu konfigurieren [4]. Konfigurationsprofis verstehen es damit unbemerkt vorgedachte Lösungen als kundenspezifische Individuallösung anzubieten. Indem sie die Produktkonfiguration geschickt nutzen, automatisieren sie die Angebotsbearbeitung oder die Erstellung von Stücklisten. Auf diese Weise entlasten sie Vertrieb und Konstruktion und schaffen die Voraussetzungen für weiteres Wachstum, denn Routineaufgaben werden mehr und mehr automatisiert.
Das Konfigurationssystem generiert dabei ein Produkt, indem es vorgedachte Komponenten auswählt, kombiniert und parametrisiert. Hierbei werden Wissen und Aufgaben in den Verkaufs- und Produktauslegungsprozess integriert und automatisiert. Konkret werden Kundenanforderungen – Merkmale und Ausprägungen wie Leistung, Drehmoment und Drehzahl – in Regeln verarbeitet und ein technisches Produkt ausgelegt.
Drei wichtige Potenzialfelder werden dabei in der Praxis adressiert:
- Prozessgeschwindigkeit und –kosten: Die Durchlaufzeiten reduzieren sich erheblich, denn Angebote und Aufträge können deutlich schneller mit weniger Aufwand erstellt werden. Dadurch werden Vertrieb und Konstruktion entlastet.
- Produktkosten und Variantenmanagement: Konfiguratoren ermöglichen eine Produktspreizung zum Markt, wobei vielfältige Lösungen aus kostenoptimierten und standardisierten Komponenten zusammengesetzt werden. Sie unterstützen so das Variantenmanagement und verhindern Wildwuchs.
- Datenqualität und Machbarkeit: Produktkonfiguratoren gewährleisten technisch und preislich hochwertige und plausibilisierte Angebote. Sie leisten damit einen aktiven Beitrag zur Fehlervermeidung und Risikominimierung.
Ursprünglich wurden Konfiguratoren für die Vertriebsunterstützung oder Stücklistengenerierung von Variantenfertigern eingesetzt. Der Schwerpunkt verlagert sich neuerdings in Richtung einer automatisierten Abwicklung sämtlicher Vertriebs- und Konstruktionsarbeiten von der Kundenschnittstelle bis zur Stückliste.
Variantenproduktion - Dynamische Produktionszyklen reduzieren Komplexität
Der beschriebene Weg der Produktstruktur- und Prozessperspektive zur Reduzierung von Durchlaufzeiten und Herstellkosten ist allerdings nicht für jede Branche anwendbar. Die Methode der Produktstrukturierung und Modularisierung wirkt nur bei zusammensetzbaren Produkten und stößt deshalb in weiten Teilen der Variantenproduktion innerhalb der Prozessindustrie wie z.B. Chemie oder Pharma schnell an ihre Grenzen, weil damit in aller Regel marktseitige Einschränkungen im Lieferprogramm einhergehen würden. Die Strategie würde in dem Fall gezielt von der Konkurrenz ausgenutzt werden. Hier bleibt nur die Möglichkeit, die vom Markt geforderte Vielfalt produktions- und lagerseitig durch intelligente Planungs- und Steuerungsmethoden zu beherrschen. Oftmals reicht dann die „Traditionelle Lagerfertigung“ nicht mehr aus. Denn die steigende Produktvielfalt treibt auch die Planungs- und Steuerungskomplexität in Produktion und Logistik. Hier sind leistungsstärkere Planungs- und Produktionsmethoden gefragt um Durchlaufzeiten zu beherrschen. Ein Erfolg versprechendes Verfahren hierbei ist die Methode „Dynamische Produktionszyklen“.
Erfahrungen aus verschiedenen Projekten in den Branchen Zulieferer, Papierindustrie, Kunststoffe verarbeitende Industrie, Chemie mit Farben und Lacke, Kabelindustrie etc. zeigen, dass Produktivitätssteigerungen von bis zu 20 % möglich sind. Zugleich kann das Lieferverhalten, vor allem die Liefertreue enorm verbessert werden.
Fallstudie: Variantenmanagement und Komplexitätsbeherrschung in der Variantenproduktion
Die Funktionsweise der Variantenfertigung bzw. der Variantenproduktion und im speziellen der Methode ""Dynamische Produktionszyklen" wird am Beispiel der Variantenproduktion eines Extrusionsunternehmens gezeigt, das aus Kunststoffen in einem kontinuierlichen Prozess die unterschiedlichen Produkte formt. Die Firma erhält zahlreiche kleine Bestellungen, muss aber auch unregelmäßig eingehende Großaufträge erledigen. Die Durchlaufzeiten und damit Lieferzeiten lagen in der Vergangenheit je nach Produkt zwischen zwei Tagen und – bei großen Mengen- mehreren Wochen.
Etwa ein Jahr nach Einführung der Planungssoftware fiel das Ergebnis nüchtern aus. Von den ursprünglich erhofften Zielsetzungen, binnen eines Jahres wenigstens die Lieferbereitschaft zu verbessern (Lieferzeiten um 20% reduzieren, Liefertreue nach OTIF - On Time In Full - von 82 % auf 93% bis 95% anheben) und die Produktivität um 10 Punkte zu erhöhen, wurde nur ein Bruchteil erreicht.
Etwas später knickte bei anziehendem Umsatz die Lieferbereitschaft drastisch auf etwa 70 % ein. Das Management plante permanent um, woraufhin die Produktivität in der Variantenfertigung weiter sank. Das Einhalten von Lieferzusagen wurde zur Glücksache. Wichtige Kunden zeigten sich unzufrieden, ein langjähriger Großabnehmer mit einem Umsatzanteil von 7 Prozent war bereits zur Konkurrenz gewechselt. Eine durchgeführte Analyse zeigte, dass es den Beteiligten auch mit Hilfe der neuen Planungssoftware nicht gelungen war, angemessen auf die ständig wachsende Komplexität in der Produktion zu reagieren. Zwar optimierten die Mitarbeiter in den einzelnen Abteilungen ihre Aufgaben jeweils richtig: der Disponent das Lager und die Lieferfähigkeit, der Fertigungsplaner die Reihenfolge der Maschinenbelegung und Losgrößen, der Vertriebsinnendienst mit Hilfe von Daten aus der Vergangenheit und Prognosen den Umsatzplan. Doch diese Einzelmaßnahmen widersprachen sich zum Teil und blieben ohne Wirkung für das Gesamtunternehmen. Die Durchlaufzeiten wurden nicht besser. Beispielsweise bedeuteten niedrigere Lagerbestände zwar eine geringe Kapitalbindung, führten aber zu einer schlechteren Lieferfähigkeit und zu kleinen Produktionslosen (und damit zum häufigen Umrüsten der Maschinen und zu weiteren Verschwendungsfaktoren). Dem Topmanagement gelang es nicht, die konkurrierenden Ziele der Abteilungen miteinander abzustimmen. Es fehlte ein geeignetes Planungsverfahren, das den veränderten Marktbedingungen und der gestiegenen Variantenvielfalt gerecht wurde.
Die Vorgehensweise
Daher wurde die Methode der dynamischen Produktionszyklen im Bereich der Variantenfertigung eingesetzt. Im ersten Schritt wurde die Nachfrage analysiert und die Produkte wurden zu Familien geordnet, je nachdem, welche Maschinen, Werkzeuge und Kapazitäten zu ihrer Herstellung nötig waren.
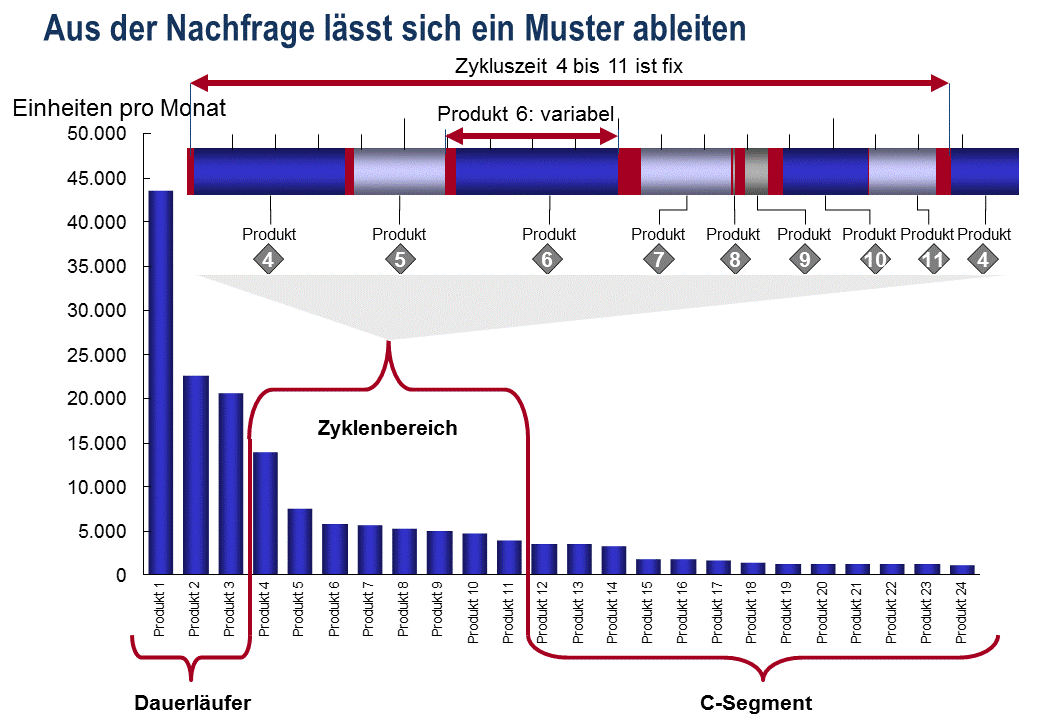
Bild 2: Dynamische Produktionszyklen, Aus der Produktnachfrage lässt sich ein Muster ableiten.
In einem zweiten Schritt wurde die optimale Abfolge ermittelt, in der die Produkte auf den einzelnen Maschinen hergestellt werden sollten. Ziel war, die Zeiten für das Umrüsten der Anlagen möglichst kurz zu halten. Die Konzentration lag dabei auf den Produkten, deren Nachfrage im mittleren Bereich lag und häufig schwankte. Gängige Produkte und solche mit konstanter Nachfrage wurden ausgeklammert, weil sich deren Fertigung leicht planen und steuern ließ. Nachdem die Abfolge an Produkten festgelegt war, wurde anhand von Nachfragedaten bestimmt, wie lang ein solcher Zyklus maximal dauerte. Ein Beispiel: Wie in Bild 2 dargestellt, sollten die Produkte 4 bis 11 immer in der Reihenfolge 4-5-6 ... 11 hergestellt werden; die Dauer eines solchen Zyklus sollte immer konstant bleiben und jeweils zwei Wochen betragen. Die Verteilung der Zykluszeit auf die Produkte 4, 5, 6 bis 11 schwankte von Zyklus zu Zyklus je nach Bedarf, etwa von wenigen Stunden bis maximal 14 Arbeitstage.
Stark vereinfacht, entspricht diese Vorgehensweise der Variantenproduktion einem Linienbusverkehr, bei dem der Bus eine fixe Route in einem festen Zyklus (Zeit bis zum nächsten Start vom Ausgangspunkt) abfährt. Die Ankunft an den Haltestellen schwankt aber, da der Bus immer so lange warten muss, bis alle Fahrgäste eingestiegen sind (übertragen auf die Produktion bedeutet dies: bis eine ausreichende Menge einer bestimmten Produktvariante gefertigt worden ist). Das Verfahren gleicht bei konstanter Gesamtkapazität (Zahl der Plätze im Bus) die zwischen den Varianten (Zahl zusteigender Fahrgäste) schwankende Nachfrage aus. Die traditionelle Lagerfertigung orientiert sich nicht in einem fixen Muster, sondern versucht immer neu, begrenzte Maschinenkapazität in einer sinnvollen Reihenfolge zu nutzen. Dies wird bei großer Variantenvielfalt und kurzer Vorlaufzeit sehr komplex. Dagegen sorgt ein dynamischer Produktionszyklus für die nötige Ruhe und Berechenbarkeit in der Fertigung, die Voraussetzung für eine hohe Produktivität ist. Weiterer Vorteil: Vor jedem Zyklus fragt die Produktion von sich aus im Vertrieb den benötigten Bedarf für die einzelnen Varianten ab. Die Größen der Fertigungslose sind von festen Vorgaben wie Mindestbestand im Lager oder Bestellzeitpunkt entkoppelt. Stattdessen passen sie sich dem Markt an. Im Beispielunternehmen stieg nach Einführung der dynamischen Produktionszyklen die Produktivität um 17 Prozent. Der Fertigungsprozess verläuft seitdem wesentlich stabiler und die Liefertreue liegt nach einem Jahr stabil bei 95 Prozent.
Wenn Sie mehr zum Thema Variantenfertigung erfahren wollen oder sich für Variantenmanagement interessieren.
Literatur
[1] Albers, S.; Klapper, D.; Konradt, U.; Walter, A.; Wolf, J. (Hrsg., 2007): Methodik der empirischen Forschung, 2. Auflage, Wiesbaden 2007.
[2] Baldwin, C. Y.; Clark, K. B.: Managing in an Age of Modularity. In. Harvard Business Review, September-October, 1997, S. 84-93.
[3] Grokamp, S.; Franke, H.-J.: Produktstrukturierung bei hoher Variantenvielfalt. In: Industrie Management 6(2007), S.33-36.
[4] Sanchez, R.: Modular architectures in the marketing process. In: Journal of Marketing, No. 63, 1999, S. 92-112.
Schlüsselwörter:
Durchlaufzeitenreduktion, Produkt- Prozessoptimierung, Produktkonfiguration, Komplexitätsmanagement, dynamische Produktionszyklen